A factory shortage is threatening the future of offshore wind in the United States, and few places illustrate the challenge better than an unfinished facility in upstate New York.
At the Port of Albany, little work has been done on a factory where 550 workers are supposed to roll thick plates of steel into massive turbine towers — the backbones of new offshore wind projects planned for the East Coast.
Trees have been cleared for the facility, but almost three years after the factory was announced, construction on its five buildings has yet to begin. And the cost of the project has more than doubled from $350 million to $700 million.
The factory’s developers insist the project will move forward, even if it won’t be done in time to serve what was supposed to be its first customer: a wind project planned off Long Island that is scheduled to begin construction as early as this year.
Even so, the developers concede they have yet to figure out how to pay for the additional expenses.
“It is a big amount of money,” said Patrick Pellerin, president of Marmen, a Quebec-based manufacturer and one of the three companies involved in the Albany factory. “We have been trying to solve that issue for quite some time.”
The problems at the Port of Albany are a microcosm of the broader issues facing offshore wind in the United States.
An overburdened supply chain has sent the cost of offshore wind projects soaring, threatening to sink several developments planned along the East Coast. The issues could kneecap the climate ambitions of coastal states from Massachusetts to Maryland and pose a stiff test of “Bidenomics” — the president’s attempt to marry emission reductions with a green manufacturing revolution.
“It’s not the most fun moment in the industry,” said Vineyard Offshore CEO Lars Pedersen, who helped shepherd America’s first major offshore wind project through permitting and to the construction phase.
Pedersen said he is fundamentally optimistic the industry will overcome its struggles but acknowledged its near-term hurdles.
“We are being impacted by things outside our control, outside the supply chain’s control and outside state governments’ or the federal government’s control, and we’re trying to navigate that,” he added. “And I think that’s what you’re seeing at the moment. And that can be painful.”
Offshore wind development is booming globally, but there are a shortage of factories that make specialized foundations, towers and blades.
Analysts say the United States cannot realize President Joe Biden’s ambition of powering 10 million homes with offshore wind by the end of the decade without a fleet of new factories. One recent study by the National Renewable Energy Laboratory concluded that the United States needs 34 domestic factories to hit the president’s target but identified only one in operation.
The lack of American factories has left the U.S. offshore industry reliant on Europe, where supply chains have been stretched by Russia’s invasion of Ukraine.
Ukraine supplied nearly half of the European Union’s steel plates, which are used to fabricate components such as towers. But its steel plate production plunged 70 percent after Russia attacked Ukrainian forces holed up in the sprawling steel mills of Mariupol, according to Rystad Energy, a consulting firm.
The supply chain crunch has forced developers to line up turbine parts years in advance and sent prices for wind projects skyrocketing. An analysis by New York regulators predicted offshore wind prices won’t return to 2022 levels this decade, as demand for key components outpaces factories’ ability to produce them.
“Even getting a slot, getting a commitment to have turbines ready by a certain date, that’s a huge issue,” said Ken Kimmell, vice president for offshore wind development in the United States for Avangrid. “On top of that, you have general inflation, and you have interest rate increases. So it’s kind of a perfect storm of a lot of different conditions that have taken us from an industry that was experiencing declining costs to one that’s now experiencing very rapid increases in costs.”
While Avangrid and its partner Copenhagen Infrastructure Partners were able to lock in contracts needed to build Vineyard Wind I, a 62-turbine project under construction south of Massachusetts, the utility’s other projects have not been so lucky.
In June, the utility paid $48 million to cancel the power contract for a Massachusetts project and negotiations with Connecticut regulators over cost increases facing another project.
Another Massachusetts project, SouthCoast Wind, paid $60 million to cancel its power deal. Two developers in New York are asking state regulators to adjust their contracts for inflation. And Ørsted pushed for legislation in New Jersey to recoup federal tax credits for a project serving the state.
Strained relationships with state officials
American factories were intended to help address many of the supply chain issues affecting the U.S. offshore wind industry. States have courted developers who included manufacturing projects as part of their wind projects.
In New Jersey, Ørsted committed to the development of a foundation factory to serve two wind projects serving the state. Down the coast in Maryland, Ørsted and U.S. Wind are tenants at a planned offshore wind manufacturing hub. In Massachusetts, an Italian company proposed building a factory making transmission cables to initially supply a project serving the state.
But few have gone as far to try and marry emission reduction and job creation as New York.
In 2020, state regulators awarded a power contract to a joint venture of Equinor and BP to build two offshore wind projects serving New York. The oil giants won the contract in part because they agreed to buy towers from the factory planned for the Port of Albany. It represented the second time New York had turned to Equinor, which won a first contract from the state in 2018.
The Port of Albany is located on the banks of the Hudson River roughly 2 miles south of the state capitol building. In the 1970s, it served as a coal ash dump for a nearby power plant. Today, businesses at the port ship everything from fuel to grain to paper.
The port’s rail access and a deep water port made it attractive for a tower factory. Five-inch thick steel plates would be delivered by train, rolled into tower segments, loaded onto barges and sent down the Hudson to Brooklyn, where they would be assembled and sent out to sea. The port had something else to offer too: 100 acres of available land to build a massive factory and an eager landlord in the Albany Port District Commission.
“If you put all these criteria together, it was extremely difficult to beat the Port of Albany as the best location,” said Marmen’s Pellerin.
The factory is a joint venture of Marmen, a maker of onshore towers, and Welcon, a Danish firm specializing in offshore towers. Equinor has been a major investor in the project, as well as the factory’s customer, while the Port of Albany has spearheaded construction.
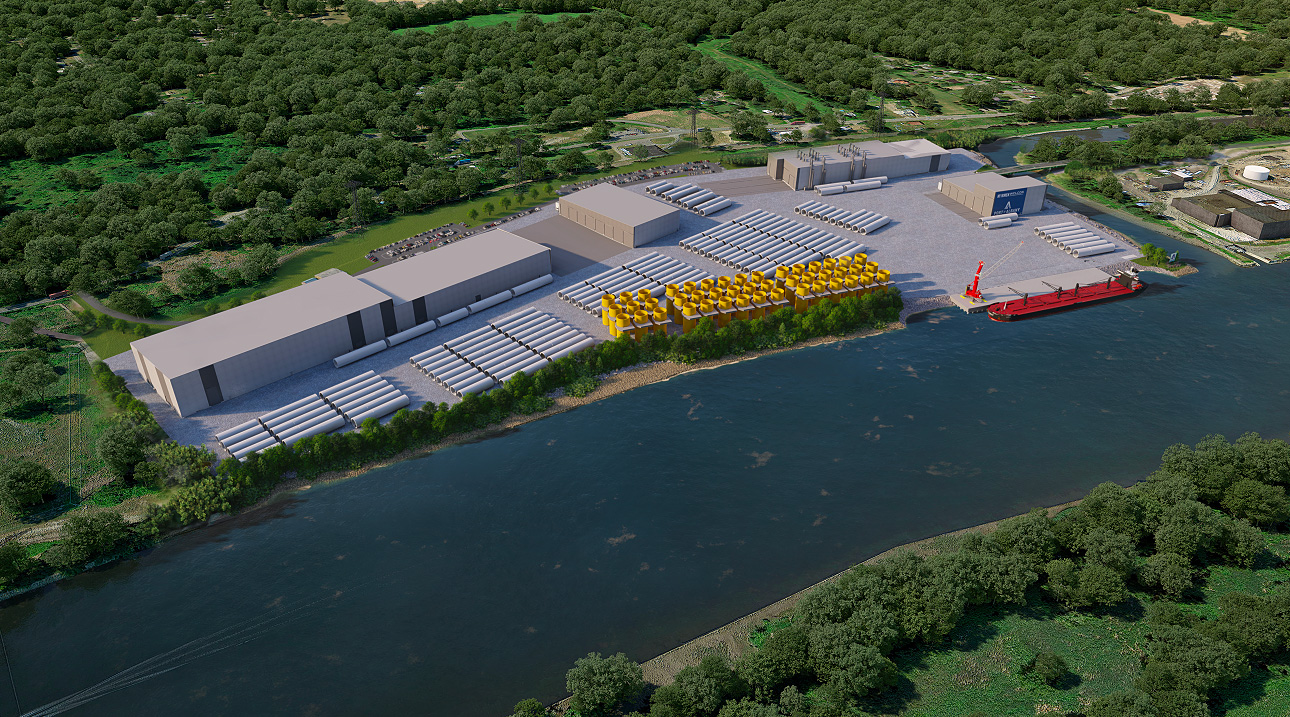
Progress has proceeded in fits and starts. Tree clearing prompted objections from some neighbors. A group of residents filed a lawsuit claiming the port had not adequately notified the public of its plans. It was later dismissed. While the project eventually succeeded in obtaining all the necessary environmental permits, costs have soared.
When the estimates of what it would cost to build the factory came in last summer, Marmen officials were shocked. What had been a $350 million factory project will now cost an estimated $700 million.
“We thought there was a mistake,” Pellerin said. “There was no mistake. That was it.”
The soaring costs have strained relationships with state officials.
During a series of emergency calls around Christmas last year, the factory’s developers pushed officials in Gov. Kathy Hochul’s (D-N.Y.) administration for help, according to people familiar with the negotiations. The state had provisionally awarded the factory a $40 million grant but declined to give more.
A spokesperson for the New York State Energy and Research Development Authority did not directly answer questions about the calls, but issued a statement saying, “NYSERDA’s grant funding was made conditional on the private parties finalizing the project’s budget and entering a binding agreement allocating funding obligations among them.”
Negotiations between the factory’s developers over how to pay for the higher costs are ongoing.
The factory might have fallen through if not for passage of the Inflation Reduction Act. The law contains tax credits for clean energy manufacturing and incentives designed to encourage wind developers to use domestic manufactured components.
While the prospect of receiving federal money has kept the tower factory alive, questions over how the tax credits will be administered have kept it from moving forward. The IRS has yet to propose rules governing the manufacturing subsidies. And even when those rules are finalized, money from the government won’t begin to flow until towers start rolling off the factory floor. The subsidies are tied to each tower produced.
Wind developers face their own issues. The Inflation Reduction Act includes a 10 percent domestic content tax credit, which wind industry officials say can help offset higher project costs. But to qualify for the credit, developers must satisfy two conditions: 20 percent of manufactured components need to be made in the United States, and all steel and iron used has to be manufactured domestically. Industry representatives said the steel requirement is particularly difficult to meet.
“It is always complex,” Pellerin said. “If it were that easy, that funding gap would already be resolved.”
‘That is a red flag’
Other factory projects planned along the East Coast are in limbo too.
In New Jersey, plans to upgrade a finishing facility, where foundations are sanded and painted, into a full-blown foundation factory are a year behind schedule due to higher costs. Maryland’s plans for an offshore wind manufacturing hub remain in their early stages.
And the fate of a cable factory in Massachusetts is uncertain after Avangrid and SouthCoast Wind paid millions of dollars to cancel power contracts with Bay State utilities. The Prysmian Group, the Italian company behind the cable factory, has said it needed assurances wind projects would move forward before committing to the facility. Prysmian officials did not return a request for comment.
In Albany, the tower factory is moving forward in a phased approach. The port has begun earth moving and site preparations in advance of construction. Equinor, in a statement, said it remained committed to the project, noting it had “contributed additional resources to the developers above and beyond the level anticipated at project conception.”
Much of the factory’s fate hinges on the outcome of developers’ request that the state pay more for their wind farms. Equinor and BP are seeking an average 54 percent increase in the prices paid to their three offshore wind projects, increasing their original price from an average of $114 per megawatt-hour to $176 per megawatt-hour. The oil giants were joined by Ørsted, which asked regulators to increase the price paid to its Sunrise Wind project from $110 per MWh to $139 per MWh.
The developers’ request to amend existing contracts has prompted questions from some state officials, including supporters of the industry. Equinor and BP’s petition comes a year after the oil companies booked record profits and returned billions of dollars to shareholders in the form of stock buybacks.
“It’s hard to know whether they’re trying to take advantage or whether this is a legitimate cost of doing business going forward,” said former New York Assemblymember Steve Englebright, a Democrat who was a leading climate hawk in the State Assembly. “I’m not ready to say this is not a good faith adjustment they are suggesting. But to suggest that if they don’t get what they want they’re going to leave, that is a red flag.”
An analysis conducted bt NYSERDA highlighted the difficult choices facing the state. It noted that the four offshore wind projects seeking revised contracts would provide 12 percent of the power needed to reach the state’s goal of achieving 70 percent renewable electricity. And it concluded some of the cost increases facing developers could not have been predicted. Without some relief, it is unlikely they will get built.
But NYSERDA also singled out Equinor and BP’s petition, saying their proposal to adjust the contracts for inflation appears to “shift risks from developers to ratepayers in a manner that goes beyond, and in some cases does not appeared tied to, the extraordinary market circumstances that underly the request.”
In a statement, Equinor said it was confronting the same challenges facing other developers in the United States. Despite the obstacles, the company said its projects “are on track to power approximately 2 million New York homes with renewable offshore wind power and support thousands of jobs and billions of dollars in economic activity while helping the state meet its renewable energy goals.”
Factory proponents said the request is a test of the state’s commitment to turn New York into a manufacturing hub for offshore wind.
“Do politicians want to go out on a limb and invest in this, even though they’re pushing it?” said Port of Albany CEO Richard Hendrick. “I’ve said you’ve committed to doing it when times were good. Now it’s getting a little rocky — I guess you can say a lot rocky — you can’t back away now. And that’s the attitude that we’ve taken at the port.”